Leather furniture is like a work of art. With our
custom made line of sofas, chairs, and ottomans, you can select the style,
color and configuration that best suits your personality.
Our all-over leather furniture is covered with 100% top
grain Argentine leather, recognized as one of the top quality furniture
leathers in the world. We do not use vinyl or split grain leathers in
manufacturing any of our products. We start with a kiln-dried hardwood
frame for lasting endurance (it's guaranteed for life!). Then we
custom cut & match our high density foam pillows to ensure even comfort
wear and durability.
We are frequently asked, "won't that take a long
time?". We have stream lined the ordering, production and
delivery process so that we deliver custom made sofas in 3 to 4 weeks.
Why is "Top Grain" so important? Read on
below about the tanning process to understand why having 100% top grain is
essential if you want lasting furniture that will hold up to use, age well, and hold it's beauty. We are confident that the
more you know about fine leather, the more you will want to order your next
leather from TruloveStyle.
The Tanning Process
|
1. Liming
A tannery does not know what kind of hide they have purchased until
the hair has been removed. The process of removing the hair is
called liming. Liming is accomplished by placing the hides in large
narrow drums, shaped like a wheel. The drums rotate for many hours
until all of the hair is removed.
|
|
2. Selection and Sorting
The hides are then sorted as to their quality. The highest quality
hides are those with the fewest markings. The least amount of work
must be done to these hides to prepare them for finishing.
|
|
3. Tanning
This process preserves the hide and makes its natural
characteristics permanent. Tanning is accomplished by placing the
hides into large rotating drums for 24 hours. These drums contain
alkaline chrome salts. The hides emerge with a slight bluish tone.
This state is called the "Wet Blue" state. This process
enables current day leather to be softer and not to crack or peal.
|
|
4. Splitting
The average thickness of a cowhide is 5mm. Upholstery leather
requires a minimum thickness of .9-1.1mm. The hides are split in a
splitting machine. This operation divides the hide in at least two
hides: the grained hide and one or two splits.
|
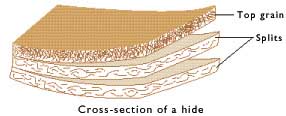 |
The strength of the fibers will vary with
these hides. The fibers are very strong on the grained hide, and get
weaker the deeper the split. The split has much less resistance and
flexibility than the grained hide. These splits are processed as
suede or embossed with graining to make it look like the grained
hide. This is done to offer a lower price on some leather furniture.
5. Finishing
A. Aniline Color: At the beginning of the
finishing process, hides are placed into the wheel shaped drums to
soften, remove excess water and apply an aniline dye. This means
that they are dyed with color all the way through. The aniline dye
penetrates completely through the entire hide. At this stage the
hides are "pure top grain aniline". These superior hides
(free from flaws) are then tumbled in drums for several hours to
give added softness. This is called milling. These hides are now
done. All other hides progress through additional surface
treatments.
B. Scar Correction - Buffing: Heavily scarred
hides must receive correction. This correction is done by feeding
them through a machine that is calibrated to the pressure needed to
smooth out the hide. The graining is, therefore, lost in the
process. These hides must later be embossed with
"graining".
C. Base Coat (Color): Hides then go through the
process of receiving a consistent color over the entire surface.
This color is close to the aniline color already received. This
enables a less apparent color contrast, if the hide somehow gets
ripped. At this point, the hide is considered protected, aniline
dyed with a base coat of color. These leathers are uniform in color
with the natural markings being covered.
D. Top Coat (Clear): These hides then go
through a clear coat finish. This seals the base color to the hide.
The color will now not rub off or be damaged.
E. Embossing: Because these hides were buffed
smooth, the next process is embossing a grain into it. This is
accomplished through heat and pressure. A hot plate is used which
has the grain pattern etched into it. Lesser quality hides receive
more buffing and embossing. With more embossing, the hide becomes
firmer and less soft to the touch. |
|
| TruloveStyle offers home furnishings and accessories from around the world that are unique, interesting, and beautiful. Our eclectic collection includes aged reproduction furniture, antiques, original arts and crafts, mirrors, lamps, floral designs, glassware, seating, tables, curios, armoires and custom leather.
Visit our showroom Mon-Sat 9 am - 6 pm
7150 Hwy 72
Cherokee, Alabama
(1 Mile East of The Natchez Trace)
We deliver/ship anywhere!
| |
|
Copyright 2001-2003 TruloveStyle. All rights reserved. Web Development by TimberLion Marketing www.timberlion.com |
|